Cell life is affected by:
- Charge Rate
- Maximum voltage
- Temperature
The cycle life is the number of complete charge/discharge cycles that the battery is able to support, and is used to measure battery lifetime.
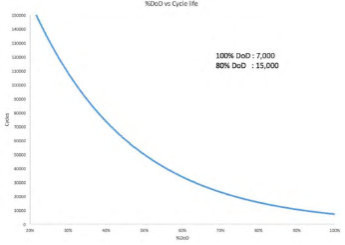
DoD vs Cycle Life – Image courtesy of Sterling PBES Energy Solutions
Charge Rate
The more charge/discharge cycles are completed, the lower the Depth of Discharge (DoD), or percentage of the energy removed from the battery.
Chemistry is a critical influencer of cycle life, and even then the detailed breakdown of the chemistry can alter the basic performance characteristics of the chemistry. Influencers like silicon can improve some aspects of performance in all chemistries, but they can also negatively impact aging, heat generation and degradation. Each chemistry relies on the integrity of its manufacturer and how “fit for purpose” it is for the markets we are applying it to.
Aging increases non-linearly with a higher charge rate (C-rate). So, the higher the C-rate, the fewer cycles the cell can undergo, reducing its lifespan.
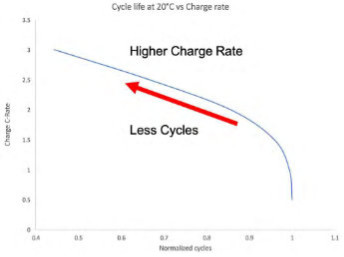
Cycle life vs C rate – Image courtesy of Sterling PBES Energy Solutions
On the other hand, Discharge rates are much less impactful than Charge rates, due to the chemical construction of the cells. On discharge, power is effectively ”allowed” to leave the battery unencumbered. We can discharge at very high rates of power; up to 10x the capacity of the system for short bursts.
But, in marine applications, we need to engineer for continuous power- and this means we limit our discharge with NMC batteries to 5C or 5 times the rated capacity of a system. SPBES can manage this generation of heat without compromising the life of the battery.
Maximum Voltage
Aging increases rapidly with higher cell voltage, even if voltage is reached only momentarily.
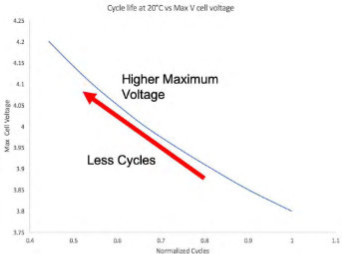
Cycle life vs Voltage – Image courtesy of Sterling PBES Energy Solutions
Temperature
Aging increases rapidly with higher cell temperatures during operation.
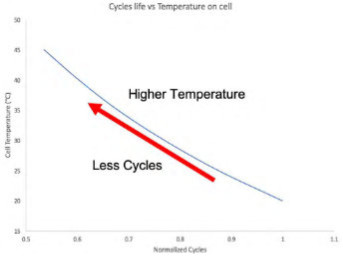
Cycle life vs Temperature – Image courtesy of Sterling PBES Energy Solutions
– Information from Sterling PBES Energy Solutions